FODS Solves an Industry Challenge
We are excited about this new method for reducing sediment track out, but we understand our clients will have questions, so here we will expand on two points made in our earlier post comparing the total cost of ownership and the effectiveness of VTCs compared to FODS.
DTEC introduced the FODS product to our clients in the fall of 2018, and we have already shared a post and dedicated a page on our website to FODS because these durable and innovative devices really will benefit our clients in most situations.
Effective Life of FODS versus VTC:
It will not be shocking or controversial to state that even at their best, traditional rock Vehicle Tracking Control installations have limited effectiveness. In theory, they are designed to be long enough for several tire rotations by vehicles leaving the bare dirt or mud of a construction project. As the tires rotate over the rock surface, the deep and loose rock surface will scrub or scrape some of the dirt/mud off of the tires, resulting in less dirt in the street. That’s the theory.
However, the rock often becomes compacted quickly and loses the ability to abrasively remove sediment from the tires of departing vehicles. When the rock surface gets clogged with mud, the loss of effectiveness is even more dramatic. On the one hand, the fact that mud is on the rock demonstrates it was effective to some degree. On the other hand, the resulting mud and rock surface quickly becomes as hard as a paved surface and therefore loses its functionality completely.
What’s the solution to refreshing this hard-packed surface? You have three options here.
- One is to use heavy equipment to scarify or churn the existing rock to loosen it up. This is reasonably cost effective, but does require having the right equipment on hand.
- The second is to bring another load of rock and spread it on top of the old layer. This is also effective for a time, but eventually has the same problems as the original installation.
- The third option, of course is to combine scarifying and new rock. In each case you are just getting temporary relief until the VTC again becomes ineffective.
To be clear, an ineffective VTC is a failed VTC. When you have to increase your sweeping frequency to compensate for a failed VTC, you are really not getting any usefulness from that method. Again, this will not be shocking to anyone in the industry. We think most experienced folks will agree the VTC is a weak point in the sediment control plan for any site.
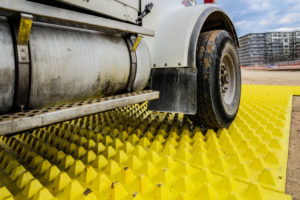
FODS Outperforms Traditional VTC
FODS, in contrast, begin their life with a much higher level of effectiveness and continue to outperform VTCs even after many months on a project. Maintenance is also significantly easier, and can restore that high level of sediment control performance quickly and easily. We continue to hear positive reviews from our clients and can attest to the durability.
To answer the question of which method is most effective at removing soil and mud from the tires of vehicles exiting a construction site, FODS are the clear winner.
Cost comparison: Consider Total Cost of Ownership
As we’ve seen with other Best Management Practices, the best way to evaluate cost is to understand the Total Cost of Ownership for a BMP on a project. Total Cost of Ownership (TCO) helps us compare apples to apples, especially when we look at all the associated costs that might be overlooked when only comparing the initial installation costs.
An initial installation cost for FODS may be in the $10K to $12K range, but will not require heavy equipment to install or maintain, will not require multiple additional loads of rock, and will greatly reduce your street sweeping budget. To summarize, from a single project TCO perspective, FODS run approximately $12K with minimal maintenance costs to be added.
Installing a rock VTC will run approximately $2000 for initial installation, and will almost certainly cost the same amount to remove, so the minimum costs start at $4K per entrance. Additional loads of rock will run $750 each, plus the scarifying or spreading, plus higher levels of street sweeping costs since the VTCs rarely work as designed. We have seen that most projects that last 6 months VTC costs can easily rack up thousands of dollars of maintenance cost and multiple thousands of dollars for street sweeping. On longer duration projects the maintenance costs multiply even faster. The single project TCO will naturally vary, but $8K to $12K is a likely range. And we are being conservative here so we won’t be accused of cooking the books to make a sale.
Wait, does this mean VTCs cost less to install and maintain? We don’t think so because we are in the construction industry for the long haul and so are you. When you relocate your FODS to a second project for almost no additional cost ($500 to move and reinstall) you’ve just won the TCO sweepstakes. Splitting the FODS costs over two projects results in a TCO cost of around $6K per project. Now FODS are an easy win compared to VTCs.
- Project 1 install / maintenance = $8,000
- Project 2 install / maintenance = $8,000
- Project 1 install / maintenance = $12,000
- Project 2 install / maintenance = $ 500
Will your FODS last for three projects? From our experience, we believe they will. FODS that are used for three or more projects become a slam dunk easy decision compared to VTC, and, I repeat AND, they will actually do the job they are designed to do.
- Project 1 install / maintenance = $8,000
- Project 2 install / maintenance = $8,000
- Project 3 install / maintenance = $8,000
- Project 1 install / maintenance = $12,000
- Project 2 install / maintenance = $ 500
- Project 3 install / maintenance = $ 500
To Summarize, if you will ever need to move an entrance at your project or if your company will have multiple projects on which to re-use them, then the FODS are clearly a TCO winner.
More reasons to select FODS

FODS – Available for Purchase or Rent
We’ve explored Effectiveness and Total Cost of Ownership as two reasons that FODS make sense for most of our clients. Please contact us if you want our help running a comparison based on your historical spending and your project type. But before we wrap up, consider these additional reasons for selecting FODS.
We have learned over the years, and at times heard directly from clients and regulators that dirt in the street is the number one reason projects will receive complaints from neighbors and the most common reason regulators will enforce stormwater regulations at construction projects. The highly visible effects of a non-performing VTC mean that you are likely to get unwanted attention very quickly if you do not manage this part of your stormwater program. In this context, FODS can save more than just money, they can avoid serious time-eating headaches on your project.
Another reason to consider FODS is that DTEC offers a rental option to make trying them easy. Maybe you want to try FODS rental to see how effective they are without making the investment in a purchase. Or maybe you don’t want to be in the business of storing FODS between projects. And you may also run shorter duration projects, in which case monthly rentals of FODS can reduce your costs even more. Whatever the case, DTEC is making it easy for you to try FODS and to experience a truly effective way to control trackout at your project.
Thanks, and we’ll see you on site.
Learn More About FODS